As seen under the major objectives of supply chain, one of the basic objectives of SCM is to make sure that all the activities and functions within as well as across the company are managed efficiently.
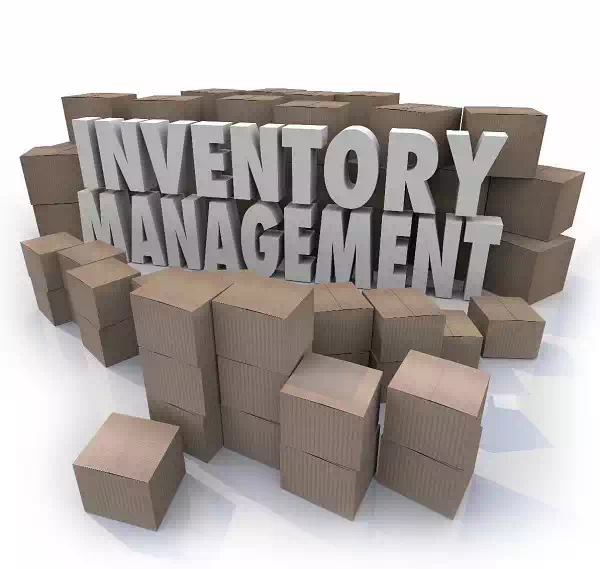
There are instances where efficiency in supply chain can be ensured by efficiencies in inventory, to be more precise, by maintaining efficiency in inventory reductions. Though inventory is considered a liability to efficient supply chain management, supply chain managers acknowledge the need of inventory. However, the unwritten rule is to keep inventory at a bare minimum.
Many strategies are developed with the objective of streamlining inventories beyond the supply chain and holding the inventory investment as low as possible. The supply chain managers tend to maintain the inventories as low as possible because of inventory investment. The cost or investment related with owning inventories can be high. These costs comprise the cash outlay that is necessary for purchasing the inventory, the costs of acquiring the inventories (the cost of having invested in inventories rather than investing in something else) and the costs related with managing the inventory.
Role of Inventory
Before understanding the role of inventory in supply chain, we need to understand the cordial relationship between the manufacturer and the client. Handling clients, coping up with their demands and creating relationships with manufacturer is a critical section of managing supply chains.
There are many instances where we see the concept of collaborative relationship being marked as the essence of supply chain management. However, a deeper analysis of supply chain relationships, especially those including product flows, exposes that at the heart of these relationships is inventory movement and storage.
More than half of it relies on the purchase, transfer or management of inventory. As we know, inventory plays a very important role in supply chains, being a salient feature.
The most fundamental functions that inventory has in supply chains are as follows β
β To supply and support the balance of demand and supply.
β To effectively cope with the forward and reverse flows in the supply chain.
Companies need to manage the upstream supplier exchanges and downstream customer demands. In this situation, the company enters a state where it has to maintain a balance between fulfilling the demands of customers, which is mostly very difficult to predict with precision or accuracy, and maintaining adequate supply of materials and goods. This balance can be obtained through inventory.
Optimization Models
Optimization models of supply chain are those models that codify the practical or real life issues into mathematical model. The main objective to construct this mathematical model is to maximize or minimize an objective function. In addition to this, some constraints are added to these issues for defining the feasible region. We try to generate an efficient algorithm that will examine all possible solutions and return the best solution in the end. Various supply chain optimization models are as follows β
Mixed Integer Linear Programming
The Mixed integer linear programming (MILP) is a mathematical modeling approach used to get the best outcome of a system with some restrictions. This model is broadly used in many optimization areas such as production planning, transportation, network design, etc.
MILP comprises a linear objective function along with some limitation constraints constructed by continuous and integer variables. The main objective of this model is to get an optimal solution of the objective function. This may be the maximum or minimum value but it should be achieved without violating any of the constraints imposed.
We can say that MILP is a special case of linear programming that uses binary variables. When compared with normal linear programming models, they are slightly tough to solve. Basically the MILP models are solved by commercial and noncommercial solvers, for example: Fico Xpress or SCIP.
Stochastic Modeling
Stochastic modeling is a mathematical approach of representing data or predicting outcomes in situations where there is randomness or unpredictability to some extent.
For example, in a production unit, the manufacturing process generally has some unknown parameters like quality of the input materials, reliability of the machines and competence within the employees. These parameters have an impact on the outcome of the manufacturing process but it is impossible to measure them with absolute values.
In these types of cases, where we need to find absolute value for unknown parameters, which cannot be measured exactly, we use Stochastic modeling approach. This modeling strategy helps in predicting the result of this process with some defined error rate by considering the unpredictability of these factors.
Uncertainty Modeling
While using a realistic modeling approach, the system has to take uncertainties into account. The uncertainty is evaluated to a level where the uncertain characteristics of the system are modeled with probabilistic nature.
We use uncertainty modeling for characterizing the uncertain parameters with probability distributions. It takes dependencies into account easily as input just like Markov chain or may use the queuing theory for modeling the systems where waiting has an essential role. These are common ways of modeling uncertainty.
Bi-level Optimization
A bi-level issue arises in real life situations whenever a decentralized or hierarchical decision needs to be made. In these types of situations, multiple parties make decisions one after the other, which influences their respective profit.
Till now, the only solution to solve bi-level problems is through heuristic methods for realistic sizes. However, attempts are being made for improving these optimal methods to compute an optimal solution for real problems as well.