From late 1970s to early 1980s, Quality is being looked at proactively and the general thought of achieving Quality always comes with a cost has disappeared. With the contributions coming from all preceding eras, Strategic Quality Management era marked the shift from product focus to customer focus, making Quality a competitive advantage. The Total Quality Control soon evolved into Total Quality Management, also known as Total Productive Maintenance, after incorporate all the previous quality elements into one whole new paradigm. The responsibility is still lying on everybody’s shoulder, but the process had transformed control to management. This evolution started to occur when managements started to realize the connection between profits and quality.
Total Quality Management
Looking at Japanese perception, by changing the way the top manager thinking is the best way to impact the company they have gained huge successes from Post World War II period to early 1970s. By competing head to head against American even in their domestic’s market, Japanese firms have gained significant consumer awareness and benchmarked as superior products with lower prices and better customer services. Americans started to realized that their lower quality products can no longer compete with the Japanese unless there are changes in how they approach. This makes them aware that their market share can be affected by the quality of their products or services, and if they do not have competitive advantages over their opponent, they will lose their sales. So, they are driven to make changes. Total Quality Management was born based on the concept of Japanese’s Company-Wide Quality Control, but the roots can still be traced back to American since most of Japanese developments are based on previous American Quality gurus. According to Schmidt and Finnigan (1992), the roots of TQM include:
· Scientific Management: Finding the best one way to do a job.
· Group Dynamics: Enlisting and organizing the power of group experience.
· Training and Development: Investing in human capital.
· Achievement Motivation: People get satisfaction from accomplishment
· Employee Involvement: Workers should have some influence in the organization.
· Sociotechnical Systems: Organizations operate as open systems.
· Organization Development: Helping organizations to learn and change.
· Corporate Culture: Beliefs, myths, and values that guide the behaviour of people throughout the organization.
· The New Leadership Theory: Inspiring and empowering others to act.
· The Linking-Pin Concept of Organizations: Creating cross-functional teams.
· Strategic Planning: Determining where to take the organization, and how and when to get there.
Schmidt et al. (1992) also proposed some outdated and incompatible theories which managements need to get rid of:
· Bureaucratic Management: Direction from top management, compliance from the lower divisions.
· Caveat Emptor: Let the buyer know beforehand.
· MBO and MBR: Management by objectives and management by results.
· Internal Competition: Encourage each department to be number one.
· The Strategy of Organizational Stability: “If it ain’t broke, don’t fix it.”
· Antagonism toward Unions: Workers’ interests are basically different from managers’ interests.
· Bottom-Line Driven: Profit leads to decision and action.
Total Quality Management operate based on 8 principles, according to Westscott (2013):
· Customer-focused: During previous era, managers are the one who decide the level of quality of the product. But in the end, customers are the one who is using the product or service, so they are the one who determine if the product or service is good enough. This mean more emphasis must be placed onto customer if you want to achieve quality.
· Total employee involvement: Continuing the Total Quality Control approach where it requires all the workforce to aim toward a common goal, by giving powers onto employees’ hands, it could increase their commitment and performances.
· Process-centered: Focus on step by step process thinking on how to produce a product or service and deliver it to customer and how to monitor process to ensure quality.
· Integrated system: Continuously improving the functions of organization with the aim to exceed the expectations of customers and the firms
· Strategic and systematic approach: strategic planning on how to integrate quality dimensions.
· Continual improvement: always making changes in order to not fall behind.
· Fact-based decision making: datamining and analysis to achieve best results.
· Communication: effective exchanges between cross-functional teams should keep employees in check with all critical changes.
Compared to the old era, Total Quality Management provides quality product or service to customers with the purpose to gain competitive advantage in the marketplace. Besterfield (1998) called the transformation from the old “a cultural change” and compared this new era with the previous one, which is summed up in Table 3.
Table 3. Cultural change after TQM adapted
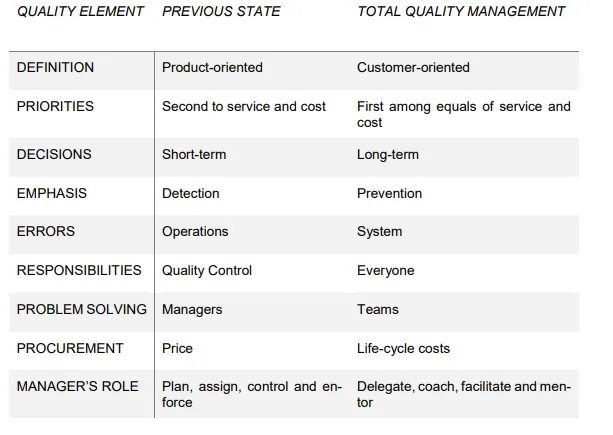
Let’s figure out how those elements are implemented to the system.