Knowing the benefits from collaboration is one hand, finding the suitable partnership that could continuously improve with each other is another hand. It is vital for the firm to find out the suitable supplier which can provide the necessary product or service quality required, so does supplier who seeking the perfect firm who could award them the most with the quality they offer. By set up a universal standard for quality, the process of identifying the correct partner will be easier. This is why certification for quality system standard are created. Some of the most notable certificate are ISO 9000 standard series, QS-9000, VDA 6.1, Malcolm Baldrige National Quality Award (BNQA), Deming Prize…
ISO 9000 family are a number of quality standards which specify the quality system capability to provide products or services which meet the customers and regulations requirements on a regular basis and the ability to achieve continuous improvements. Officially published in 1987, the standard origin is dated in 1980, where the technical committee 176 is formed with the purpose of “Standardization in the field of quality management (generic quality management systems and supporting technologies), as well as quality management standardization in specific sectors at the request of the affected sector and the ISO Technical Management Board.” The standard has gone through multiple revisions, and the latest version is in 2015. EN-29000 European standard and Q9000 American standard are considered the same to ISO 9000. ISO 9000 family standard series contain 4 standards:
· ISO 9001:2015: Quality management systems Requirements
· ISO 9000:2015: Quality management systems – Fundamentals and vocabulary (definitions)
· ISO 9004:2009: Quality management systems – Managing for the sustained success of an organization (continuous improvement)
· ISO 19011:2011: Guidelines for auditing management systems
While ISO 9000 are not available for individuals and organizations to certify, and ISO 9001 is the only standard which can be registered, we will focus more on the ISO 9001 standard.
The concept of the ISO 9001 standard is based on MIL-Q-9858A standard, which was published in 1963 by United States’ Department of Defense. The standard can be applied to any organizations which are qualified, regardless of their scale and where they operate. In order to acquire the certificate, organizations must prove that they follow the seven quality management principles: customer-oriented, management responsibility, employee engagement, process approach, continuous improvement, evidence based decision making, relationship management. The relation between these principles can be related to the process-based plan-do-check-act model below.
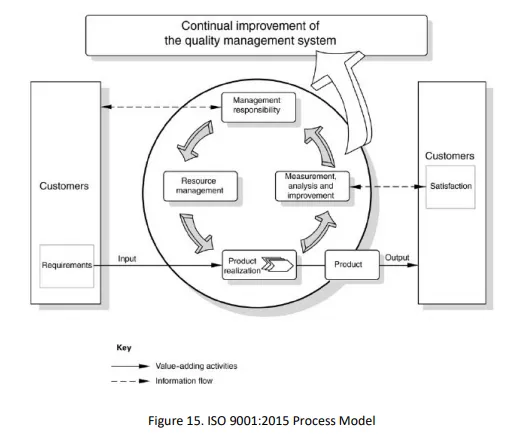
Even though not all of the principles are shown on the model, it still demonstrates the emphasis on customers and the involvement of all departments. These seven principles are pretty similar to the Malcolm Baldrige criteria for performance excellence, except for the process approach, which is replaced by results, making the award focuses more on performance and innovation, moving toward benchmarking rather than being a world-wide recognition standard for quality system. Driven by Feigenbaum’s ideology, Malcolm Baldrige National Quality Award are going further than ISO 9000 when taking into account the customer satisfaction, while ISO 9000 only put emphasis on the results of their system.
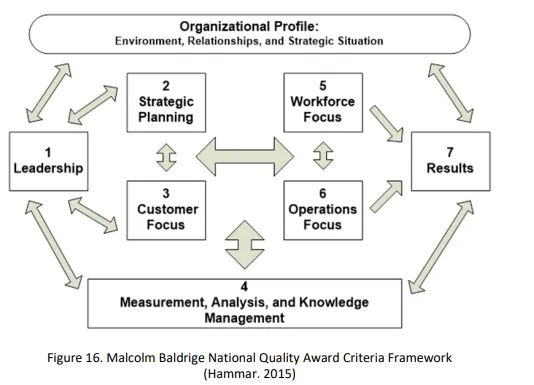
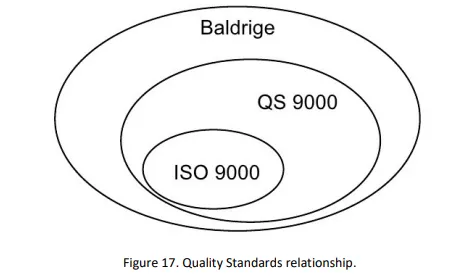
There are also quality standards which are dedicated for the automobile industries such as VDA 6.3, QS-9000, SAE,… but these quality standards still serve one goal, which is to award organizations which has prominent quality management system in place.