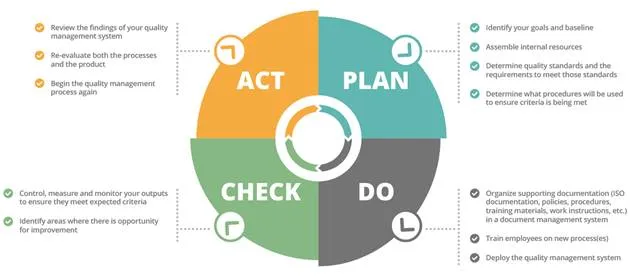
Quality control (QC) is a process through which a business seeks to ensure that product quality is maintained or improved. Quality control requires the business to create an environment in which both management and employees strive for perfection. This is done by training personnel, creating benchmarks for product quality and testing products to check for statistically significant variations.
A major aspect of quality control is the establishment of well-defined controls. These controls help standardize both production and reactions to quality issues. Limiting room for error by specifying which production activities are to be completed by which personnel reduces the chance that employees will be involved in tasks for which they do not have adequate training.
Understanding Quality Control
Quality control involves testing of units and determining if they are within the specifications for the final product. The purpose of the testing is to determine any needs for corrective actions in the manufacturing process. Good quality control helps companies meet consumer demands for better products.
Quality testing involves each step of the manufacturing process. Employees often begin with the testing of raw materials, pull samples from along the manufacturing line and test the finished product. Testing at the various stages of manufacturing helps identify where a production problem is occurring and the remedial steps it requires to prevent it in the future.
The quality control used in a business is highly dependent on the product or industry. In food and drug manufacturing, quality control includes ensuring the product does not make a consumer sick, so the company performs chemical and microbiological testing of samples from the production line. Because the appearance of prepared food affects consumer perception, the manufacturers may prepare the product according to its package directions for visual inspection.
In automobile manufacturing, quality control focuses on the way that parts fit together and interact and ensuring engines operate smoothly and efficiently. In electronics, testing might involve using meters that measure the flow of electricity.
The Techniques of Quality Control
There are several methods of measuring the performance of quality control. A quality control chart is a graphic that depicts whether sampled products or processes are meeting their intended specifications—and, if not, the degree by which they vary from those specifications. When each chart analyzes a specific attribute of the product it is called a univariate chart. When a chart measures variances in several product attributes, it is called a multivariate chart.
Randomly selected products are tested for the given attribute or attributes the chart is tracking. A common form of a quality control chart is the X-Bar Chart, where the y-axis on the chart tracks the degree to which the variance of the tested attribute is acceptable. The x-axis tracks the samples tested. Analyzing the pattern of variance depicted by a quality control chart can help determine if defects are occurring randomly or systematically.
The Taguchi Method of quality control is another approach that emphasizes the roles of research and development, product design, and product development in reducing the occurrence of defects and failures in products. The Taguchi Method considers design to be more important than the manufacturing process in quality control and tries to eliminate variances in production before they can occur.
The Role of Quality Control Inspectors
Quality control inspectors protect the consumer from defective products and the company from damage to its reputation due to inferior manufacturing processes. If the testing process reveals issues with the product, the inspector has the option of fixing the problem himself, returning the product for repairs or tagging the product for rejection. When issues arise, the inspector notifies supervisors and works with them to correct the problem.