Let’s add two more activities to our example: procurement and material handling. The costs of these two activities are not caused by—nor do they correlate with—machine hours. Rather, we will assume that both of these activities are related to the physical weight of the direct material used in making the product.
The company determines that $300,000 of its annual manufacturing overhead is associated with procurement and material handling. As a result, the company removes $300,000 from the manufacturing overhead that will be allocated via machine hours, and instead plans to allocate the $300,000 to the products based on the weight of the materials used. The company expects that during the year it will procure and handle 3,000,000 pounds of material. Under activity based costing, the company will assign $0.10 ($300,000 divided by 3,000,000 pounds) per pound of product weight to each unit manufactured. The end result is that the heavier parts will not only have more direct material cost, they will also be assigned more factory overhead than the lighter parts. By assigning some manufacturing overhead to a product based on the product’s weight, the remaining manufacturing overhead assigned via machine hours will be reduced. These points are illustrated in the following table:
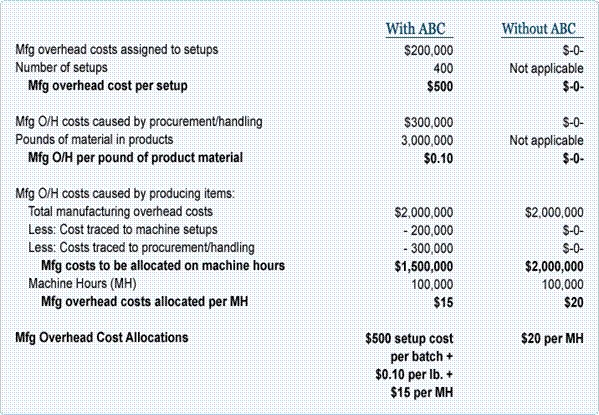
In the table below we can see how ABC would assign costs to the following:
- A product that weighs 0.5 pound and is produced in a batch of 50,000 units at a rate of 50 per hour.
- A product that weighs 1.5 pounds and is produced in a batch of 50,000 units at a rate of 50 per hour.
- No activity based costing allocations—all manufacturing overhead costs are allocated entirely via machine hours.
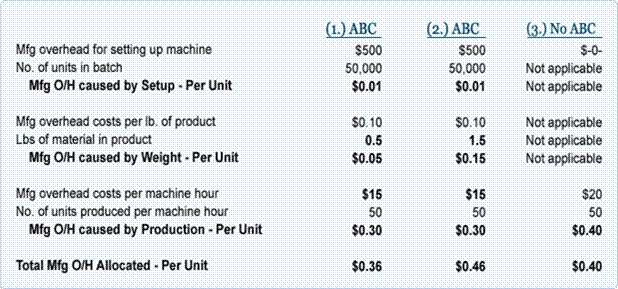
If the manufacturing overhead costs are caused by a number of activities such as setup, procurement, handling, and production, then using the activity based costing method of determining costs will give you a result that is closer to the true costs. As you can see, the product that weighs 0.5 pound is assigned $0.36 of manufacturing overhead, while the product weighing 1.5 pounds is assigned $0.46 of manufacturing overhead. Under the traditional costing allocations the procurement and handling costs would be assigned on production hours. Keep in mind that whenever manufacturers have a diverse lineup of products, allocating costs on a single basis (such as machine hours) will result in inaccurate per-unit manufacturing overhead costs.
Please Note…
You should consider our materials to be an introduction to selected accounting and bookkeeping topics, and realize that some complexities (including differences between financial statement reporting and income tax reporting) are not presented. Therefore, always consult with accounting and tax professionals for assistance with your specific circumstances.
Comments are closed