A team may work on multiple and overlapping projects. The estimated time and the manner to accomplish the projects may be planned and monitored as cumulative man-hours. Different performance benchmarks may be utilized for man-hour capacity planning. A man-hour is defined as a quantifiable unit of continuous work, which can indicate performance of work (or merely time spent), and thus is normally used to charge and bill for work done. Capacity planning should consider estimates, known factors and unknown factors in determining man-hours available for acquisition and assignment of work.
Man-hour capacity may be determined for a month, a year or for any specified duration with clear start and end dates. Generally, man-hour capacity is determined from man-days available, such as when planning capacity for the start of a new year.
Man-days available for a year, of a single resource, may be determined easily: 365 days minus non-working weekend days (104 days), minus annual national holidays (10 days), and deduct planned vacation days (say 20 days). In this example: 231 man-days are available from the single resource for the year, which can be contracted outward. Assuming an average of eight hours of effort in a day is possible (about 40 work hours a week), the single resource will contribute a total of 1,848 gross man-hours for the year.
Therefore, a three-man team arguably should be able to accomplish over 5,500 man-hours of work for the year in planning (assuming each resource works 40 hours a week and takes 20 vacation days). This figure is not realistic; the gross man-hours or man-days estimated for the team should deduct time for the following, which include:
● Personal development (e.g., formal training)
● Unplanned leave (e.g., falling sick)
● Trade events (e.g., attending business conferences or technical workshops)
● Unknown events (e.g., systems failure at a client requiring time away from assigned tasks)
● Unrelated activities such as participating in pre-sales or preparing tender documents (e.g., in support of the sales and marketing team)
Allocation for personal development is commonly defined as a policy; e.g., a minimum of five days for each resource on company-sponsored training (resulting in a reduction of 15 man-days from the three-man team). Personal development may include formal social events that are sanctioned by the company [e.g., five days a year for the team (an annual event with one activity each quarter)].
The number of man-hours or man-days to allocate for attending trade events may be gleaned from past records or from scheduled trade conferences or technical workshops, including planned networking meetings. Man-hours or man-days to be deducted may include aggregated figures from previous month statistics—on unplanned leave, in dealing with unknown or unexpected events and for participating in activities not related to core activities.
Time may also be allotted for mandated rest (e.g., time away from a computer monitor or visual displays). There are other factors too that will reduce available capacity (e.g., time for team “forming” and “storming,” especially when plans are afoot and recruiting team members are in progress).
In a nutshell, capacity planning for a team will account for the total available man-hours or man-days of a specified duration with planned and unplanned activities. Provision for unplanned activities may be aggregated from past records, typically over 12 months or of a corresponding period.
Table 1 exemplifies capacity planning for a client in the last quarter of a certain year. The data is from a three-person team working on multiple and overlapping projects. The projected hours for all projects are treated as cumulative, and the team is free to define tasks for themselves: what they would do, and how they would complete their assigned tasks:
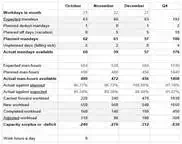
Table 1: A simple capacity planning worksheet
The shaded rows of the table require input from a project manager. The input parameters are defined separately (on different worksheets). How exactly each parameter (e.g., new workload) may be determined and defined on associated worksheets is beyond the scope of this article.
The following parameters may be filled as when available for the months ahead:
● Expected mandays: A resource is hired with certain expectations. This could be the number of days a resource is expected to supply to production. For a team, the expected man-days is the cumulative total of man-days the team is expected to contribute to production. It is a sum of expected days (and not total resources multiplied by workdays of a month), because resources may leave and join the team at any time within the said month. In the example, the “expected man-hours” are derived from the contracted duration of work (e.g., eight hours in a day.
● Planned deduct man-days: The man-days to deduct from expected man-days of the month. These are days that will reduce man-days available for production, which include official national holidays, scheduled business meetings, planned company social activities, booked training workshops, allotted time away from workstation, committees, etc.
● Planned off days: Similar to above, these are days to deduct from expected man-days of the month, but which are not determined by the company. These may include vacation leave days (entitlement), union meetings, etc.
The “planned man-days” represent the capacity available for the month having accounted for non-production days (assuming there are no interruptions). Thus, the “planned man-hours” is similarly derived.
The following parameters are filled at the beginning of a new month for the immediate past month. These are data captured and validated for that past month:
● Unplanned days: These are unanticipated impacted days or days lost (e.g., from sick leave or absenteeism). It can be due to any other event or incidence that will reduce planned man-hours. This data is captured after closing the month, to reflect on “actual man-days available” and “actual man-hours available” for production.
● New workload: This parameter captures estimated man-hours required to complete all new projects received for the month. It assumes work is received or assigned mostly at the beginning of the new month, and work is not rolling in throughout the month.
● Completed workload: This parameter captures actual man-hours spent on planned tasks completed in the month. Table 2 exemplifies completed man-hours for November:
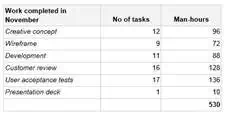
Table 2: Completed workload recorded on different worksheet
● Adjusted workload: This parameter records planned or assigned man-hours (i.e., tasks that are not completed in the month). The parameter may be used to adjust the man-hours of tasks to bring forward to the next month (e.g., from re-estimating the duration required on outstanding work).
At the start of each month, performance data is concluded on:
● Work carried forward from the previous month
● Work completed in the previous month
● Work started (i.e., new assignments in the previous month)
● The adjusted or work still outstanding from re-estimates
A positive “capacity surplus or deficit” parameter will indicate the team is able to take on more work, while a negative figure will indicate the team may be short on resources. The latter will impact the capacity available in the forthcoming month, reflected as outstanding man-hours in “carried forward workload.”
The worksheet template accompanying this article is used to determine man-hour capacity for the months ahead, and record accomplishment of past months. The worksheet tool may be utilized to:
● Determine capacity available to compete for work or assignments
● Track completed man-hours or man-days against estimates to develop “expert judgment” capabilities in estimating man-hours requirements for new projects. This is a team effort to rationalize project determinants and refine estimating projects intuitively with actual figures from completed projects against estimates at the start of the same projects.
● Indicate capacity utilization and performance of the team