The control chart is a graph used to study how a process changes over time. Data are plotted in time order. A control chart always has a central line for the average, an upper line for the upper control limit, and a lower line for the lower control limit. These lines are determined from historical data. By comparing current data to these lines, you can draw conclusions about whether the process variation is consistent (in control) or is unpredictable (out of control, affected by special causes of variation). This versatile data collection and analysis tool can be used by a variety of industries and is considered one of the seven basic quality tools.
Control charts for variable data are used in pairs. The top chart monitors the average, or the centering of the distribution of data from the process. The bottom chart monitors the range, or the width of the distribution. If your data were shots in target practice, the average is where the shots are clustering, and the range is how tightly they are clustered. Control charts for attribute data are used singly.
· When to use a control chart
· Basic procedure
· Create a control chart
· Control chart resources
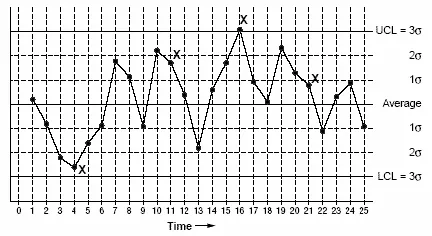
Control Chart Example
· When controlling ongoing processes by finding and correcting problems as they occur
· When predicting the expected range of outcomes from a process
· When determining whether a process is stable (in statistical control)
· When analyzing patterns of process variation from special causes (non-routine events) or common causes (built into the process)
· When determining whether your quality improvement project should aim to prevent specific problems or to make fundamental changes to the process
v Choose the appropriate control chart for your data.
v Determine the appropriate time period for collecting and plotting data.
v Collect data, construct your chart and analyze the data.
v Look for “out-of-control signals” on the control chart. When one is identified, mark it on the chart and investigate the cause. Document how you investigated, what you learned, the cause and how it was corrected.
Out-of-control signals
Ø A single point outside the control limits. In Figure 1, point sixteen is above the UCL (upper control limit).
Ø Two out of three successive points are on the same side of the centerline and farther than 2 σ from it. In Figure 1, point 4 sends that signal.
Ø Four out of five successive points are on the same side of the centerline and farther than 1 σ from it. In Figure 1, point 11 sends that signal.
Ø A run of eight in a row are on the same side of the centerline. Or 10 out of 11, 12 out of 14, or 16 out of 20. In Figure 1, point 21 is eighth in a row above the centerline.
Ø Obvious consistent or persistent patterns that suggest something unusual about your data and your process.
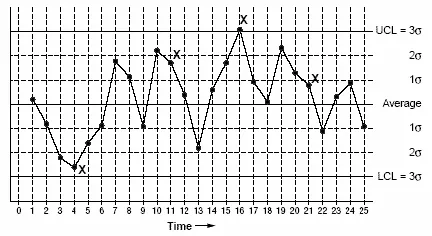
Figure 1 Control Chart: Out-of-Control Signals
v Continue to plot data as they are generated. As each new data point is plotted, check for new out-of-control signals.
v When you start a new control chart, the process may be out of control. If so, the control limits calculated from the first 20 points are conditional limits. When you have at least 20 sequential points from a period when the process is operating in control, recalculate control limits.